Steam Usage at EPS Production
Expanded Polystyrene, or EPS for short, is a lightweight, rigid, plastic foam insulation material produced from solid beads of polystyrene. Expansion is achieved by virtue of small amounts of pentane gas dissolved into the
polystyrene base material during production.
polystyrene base material during production.
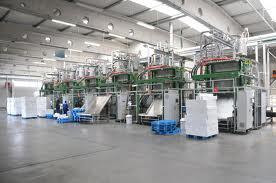
Expanded Polystyrene, or EPS for short, is a lightweight, rigid, plastic foam insulation material produced from solid beads of polystyrene. Expansion is achieved by virtue of small amounts of pentane gas dissolved into the
polystyrene base material during production.
polystyrene base material during production.
The gas expands under the action of heat, applied as steam, to form perfectly closed cells of EPS. These cells occupy approximately 40 times the volume of the original polystyrene bead. The EPS beads are then moulded into appropriate forms suited to their application.
Air replaces pentane gas in EPC cells so that 98 % percentage of EPS consists of air. This property of EPS makes it a good packing material because of lightness and insulation material because of big heat rezistance.
EPS production consists of fife manufacturing stages:
-
Pre-expansion : Polystyrene granules are expanded by free exposure to steam to form larger beads, each consisting of a series of non-interconnecting cells.
-
Conditioning : After expansion, the beads still contain small quantities of both condensed steam and pentane gas. As they cool, air gradually diffuses into the pores, replacing, in part, the other components.
-
Moulding : The beads are moulded to form boards, blocks or customised products. The mould serves to shape and retain the pre-foam, and steam is again used to promote expansion. During moulding, the steam causes fusion of each bead to its neighbours, thus forming a homogeneous product.
-
Shaping : Following a short cooling period, the moulded block is removed from the machine, and after further conditioning, may be cut or shaped as required using hot-wire elements or other appropriate techniques.
-
Post-production processing : The finished product can be laminated with foils, plastics, roofing felt, fibreboard or other facings such as roof or wall cladding material.
We are interested in a part of this process wher steam is used.
EPS production process needs between 6 to 8 bar of steam.
Steam consumtion in EPS process ranges from 15 kg to 25 kg per cubic meter of manufactured EPS block.
The steam consumption per cubic meter of manufactured EPS drops while block volume of manufactured EPS grows. This steam amount is a value determined for each loop. To calculate hourly steam consumption, this steam consumption value is multiplied with loop number in an hour.
Steam consumption in EPS production reaches a pik point in every loop and drops to zero after heating completes. That means, steam consumption during process draws a sinus curve with ups and downs. That causes steam boiler load changes between a minimum and a maximum load in every cycle. In this case steam boiler capacity should be selected according to max. steam load. However steam boiler can not reply to max. steam demand of process in seconds.
The best way to balance between steam demand of EPS process and steam production of steam boiler is using of A STEAM ACCUMULATOR at steam plant. So that, excess steam can be accumulated in steam accumulator when steam consumtion in process drops. And steam accumulator can give additional steam when steam consumption is pik period. Steam accumulator lets boiler runs at a mean load. So boiler capacity can be chosen according to average load instead of max. load by using of steam accumulator.
Boiler operation pressure should be higher than the pressure required by EPS process for using of steam accumulator effectively. Boiler operation pressure and steam accumulator volume should be chosen proportionally according to steam consumption of EPS production in every cycle. If it is necassary to give an example, boiler operation pressure should be chosen as 10 bar or 12 bar where EPS process requires 6 bar of steam. In this case steam boiler charges steam accumulator up to 12 bar when steam consumption in process drops and steam accumulator offers extra steam by using a pressure reducer until accumulator pressure drops to 6 bar when process steam consumption reaches pik period. But boiler load remains stabile in every cycle because steam consumption is balanced by steam accumulator.
The explanation given above clearly shows steam plant for EPS production should be designed by calculating steam accumulator volume and boiler operation pressure in proportion before making investment.
You can read our article "CAN STEAM BE STORAGED EVEN?" for usage of steam accumulator. Unfortunatelly it is available only in Turkish for now.
You can also feel yourself free to consult ARALSAN before, during or after design stage of your EPS production investment.
All rights of this page is reserved by Mustafa Aral and ARALSAN. It can not be copied in any way. But a quote can be made only by indicating clearly the source by writing "It is quoted from web site www.aralsan.com ".